8-Apr-2025
Unmanned crane for bulk material grab bucket – intelligent transformation plan for grab bucket crane
Industry Pain Points and Digital Breakthroughs
1. Core Pain Points of Traditional Operations
In heavy industries such as salt chemicals, metallurgy, and building materials, bridge grab cranes have long been plagued by the following issues:
(1) Low Manual Efficiency, Production Bottlenecks
- Dependence on Skilled Operators: Traditional crane operation requires 3-5 years of experience, with long training cycles and high staff turnover.
- Discontinuous Operations: Shift changes and worker fatigue result in equipment utilization rates below 60%, disrupting production flow.
- Low Precision: Manual handling of bulk materials like limestone leads to spillage and underfilled grabs, with actual loading rates of only 70%-80%.
(2) Labor Shortages in Hazardous Environments, Soaring Costs
- Harsh Working Conditions: High dust and noise levels increase occupational disease risks, making jobs unattractive.
- High-Altitude Hazards: Operators must climb cabins over 20 meters high, with unavoidable fall risks.
- Worsening Labor Shortage: A Jiangsu customer reported: “Even with ¥8,000 monthly salaries, qualified operators are hard to find, and post-90s employee retention is below 30%.”
(3) Persistent Safety Risks
- Rope Failures: Skewed pulls cause derailments and breakages, with annual maintenance costs exceeding ¥150,000.
- Collision Risks: Human judgment errors lead to equipment collisions, averaging one shutdown per quarter for repairs.
- Slow Emergency Response: Manual fault reporting delays resolutions, averaging 4 hours per incident.
(4) Outdated Management, Low Digitalization
- Experience-Based Scheduling: Paper-based task assignments result in 40% information delays.
- Data Black Box: Lack of equipment runtime data makes failure prediction and energy optimization impossible.
- Poor Coordination: Siloed warehouse, logistics, and production systems lead to 20% lower inventory turnover than industry averages.
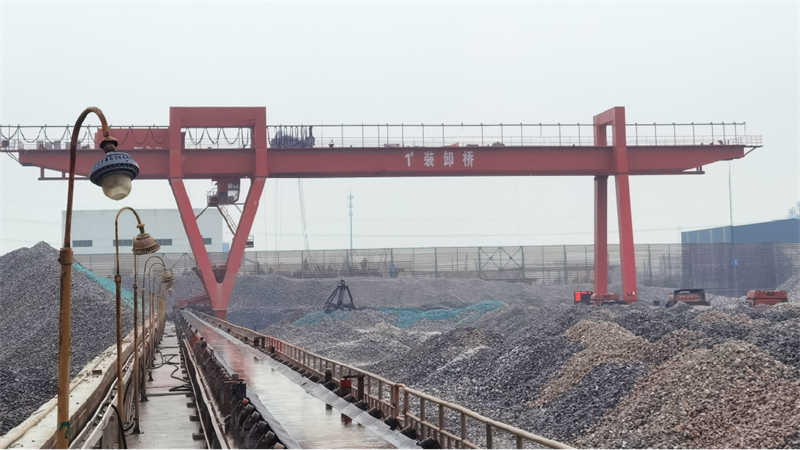
2. Digital Crane’s Breakthrough Solution
To address these challenges, Digital Crane delivers a “Hardware Upgrade + System Empowerment + Management Evolution” integrated solution:
(1) Efficiency Revolution: From “Manual” to “Intelligent”
- Unmanned 24/7 Operation: Equipment utilization rises to 85%+.
- Smart Grab Algorithm: 3D-scanned pile morphology enables optimal grab paths, stabilizing loading rates above 95%.
- Multi-Crane Coordination: One operator manages 3 cranes simultaneously, increasing handling capacity from 50 to 65 tons/hour.
(2) Safety Reinvention: From “Human Watch” to “Tech Guard”
- Three-Tier Protection:
- Equipment Layer: Real-time rope monitoring and motor overheating protection with auto-shutdown.
- Spatial Layer: LiDAR + UWB positioning achieves centimeter-level collision avoidance.
- System Layer: AI predictive maintenance with ≥95% fault warning accuracy.
- Eliminated High-Risk Scenarios: Remote control removes exposure to heights, dust, and noise.
(3) Management Evolution: From “Vague” to “Precise”
- End-to-End Visualization: 3D digital twin displays real-time equipment status, inventory, and progress.
- Smart Work Order System: Automated MES task assignment cuts dispatch time from 30 to 5 minutes.
- Data Asset Utilization: Runtime analytics generate efficiency reports for process optimization.
Customer Value Comparison (Jiangsu Salt Chemical Case)
Metric | Pre-Upgrade | Post-Upgrade | Improvement |
---|---|---|---|
Staff per Shift | 5 | 1 | ↓80% |
Energy per Ton | 2.8kWh | 2.3kWh | ↓18% |
Monthly Failures | 3 | 0.5 | ↓83% |
Inventory Turnover | 15 days | 11 days | ↑27% |
Digital Crane isn’t just a system—it’s a revolution in production methodology!
(Note: All data comes from verified implementations in the Jiangsu salt chemical industry.)
In-Depth Analysis of the Digital Crane Core Solution
1. Automated Control System—The “Intelligent Core” of the Jiangsu Project
- High-Precision Positioning System (UWB + Laser): Achieves ±3cm positioning in complex limestone pile environments, solving the “inaccurate grabbing” issue of traditional cranes
- Dual Rope Protection:
- Anti-Skew Pull System: Corrects operations with deviation angles >5° in real-time, reducing rope wear by 50% at the customer site
- Anti-Derailment Control System: Combines tension monitoring and mechanical limits to eliminate derailment risks entirely
- Intelligent Grab Loading Algorithm: Adjusts bucket opening based on material pile morphology, increasing fill rate from 78% to 97% in customer tests
2. Ground Remote Control—The “Smart Hub” of the Salt Chemical Plant
- 3D Visualization Platform: Displays real-time warehouse status (as shown in visuals), including inventory levels, equipment locations, and task progress
- Multi-Crane Coordination: Originally required 3 operators for 2 cranes; now, 1 person in the control room can complete the entire limestone handling process
3. Logistics and Safety Management—Tangible Value for Customers
- AI Safety Management System:
- Intrusion Warning: Automatic emergency stop within 5 seconds, 8x faster than manual response
- Equipment Health Monitoring: Early warnings for issues like motor overheating, reducing failure rates by 60%
- Digital Maintenance Dashboard: Customer feedback: “Maintenance cycles have shifted from ‘fixed intervals’ to ‘on-demand,’ cutting annual costs by 35%.”
Why Choose Digital Crane?
🔹 Industry Expertise: Customized solution based on 6 on-site surveys, tailored to salt chemical material characteristics
🔹 Quantifiable Benefits:
- Labor Costs: Reduced from 5 workers to 1, saving ¥820,000 annually
- Energy Optimization: Frequency control + path planning cut electricity costs by 18%
🔹 Rapid Replication: Successfully deployed in soda ash, fertilizer, and other salt chemical scenarios
Customer Testimonial
“The transformation not only solved our hiring challenges but also elevated our logistics management from ‘experience-driven’ to a new era of ‘data-driven’ operations!”
—Production Director, Jiangsu Salt Chemical Enterprise