18-Mar-2025
63/20t Double Girder Overhead Travelling Crane: A Comprehensive Guide for Singaporean Industries
The 63/20t double girder overhead travelling crane, with a span of 25.5m, is a critical piece of heavy industrial equipment that plays a pivotal role in modern manufacturing, logistics, and port operations. In Singapore, a global hub for trade and logistics, this crane is indispensable for ensuring efficient material handling and maintaining the country’s competitive edge in industrial production. Its structural design not only impacts the efficiency and safety of lifting operations but also reflects the level of advanced manufacturing technology. This guide provides a detailed overview of the crane’s design principles, structural composition, force analysis, material technology, and safety features, tailored to the needs of Singaporean industries.
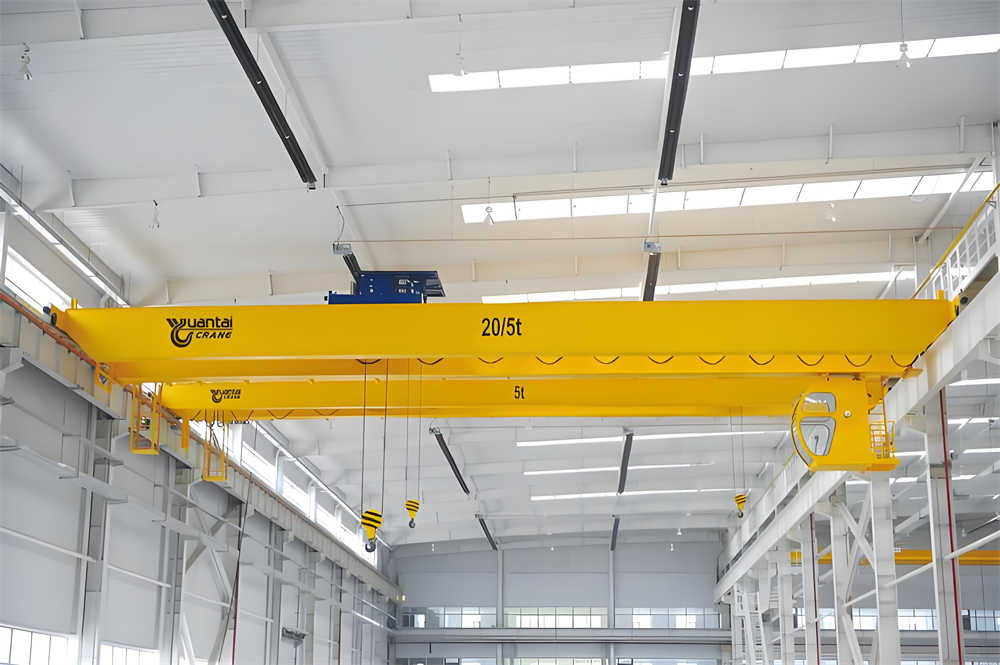
1. Crane Overview
The double girder overhead travelling crane is a leader in heavy machinery, designed to handle heavy loads with precision and stability. Its unique structure consists of two parallel main girders connected by end girders, forming a robust frame that moves horizontally along tracks. This design ensures high stability, safety, and efficiency, making it ideal for Singapore’s demanding industrial environments, such as ports, logistics parks, and manufacturing facilities.
Key Features:
- High Load Capacity: Rated at 63/20t, suitable for heavy lifting operations.
- Wide Span: 25.5m span allows for handling large containers and cargo.
- Flexibility: Customizable lifting height and operating speeds to meet specific needs.
- Work Class: A5 work class, suitable for frequent and heavy-duty operations.
2. Application Scenarios in Singapore
In Singapore, the double girder overhead crane is widely used in:
- Ports and Terminals: For efficient container handling at facilities like PSA Singapore.
- Logistics Parks: For moving heavy cargo in confined spaces.
- Manufacturing Plants: For lifting heavy machinery and materials in industries such as shipbuilding and aerospace.
- Construction Sites: For handling large structural components.
The crane’s design is optimized to withstand Singapore’s unique environmental conditions, such as high humidity, temperature fluctuations, and corrosive coastal air.
3. Design Principles and Standards
Design Principles
The crane is designed with the core principles of safety, reliability, efficiency, and economy. Key considerations include:
- Structural Stability: Ensured through advanced finite element analysis (FEA) and high-strength materials.
- Operational Efficiency: Achieved through optimized lifting and travel mechanisms.
- Safety Features: Integrated safety devices such as overload protection, anti-collision systems, and emergency brakes.
Compliance with Standards
The crane adheres to international and Singaporean standards, including:
- Crane Design Code (GB/T 3811): Specifies requirements for structural design, material selection, and safety.
- Crane Safety Regulations (GB 6067): Ensures safety in design, manufacturing, installation, and operation.
- ISO Standards: For quality management and environmental sustainability.

4. Structural Composition and Component Design
Main Girder Design
The main girder, the core load-bearing component, is designed as a box structure for high strength, stiffness, and stability. It is made from high-strength low-alloy steel and undergoes heat treatment to enhance durability.
Secondary and End Girder Design
The secondary and end girders provide additional support and stability. They are designed with reinforced structures and high-strength bolts to ensure secure connections.
Lifting Mechanism
The lifting mechanism, available as an electric hoist or winch, is customizable to meet specific operational needs. It includes features like speed control, braking systems, and limit switches for safety.
Operating Mechanism
The trolley and bridge operating mechanisms ensure smooth horizontal movement. They are equipped with high-performance motors, reducers, and wheel arrangements for stability and precision.
5. Force Analysis and Stability Assessment
Static and Dynamic Force Analysis
- Static Analysis: Ensures the crane can handle maximum loads without deformation or failure.
- Dynamic Analysis: Evaluates the impact of dynamic loads during startup, braking, and operation to prevent resonance or instability.
Stress and Deformation Calculations
Advanced FEA software is used to simulate stress distribution and deformation under maximum load conditions, ensuring compliance with safety standards.
Stability and Safety Assessment
The crane’s stability is assessed to prevent tipping or slipping. Safety devices like anti-tipping and anti-slip systems are integrated to enhance operational safety.
6. Material Selection and Manufacturing Processes
Material Selection
- High-Strength Steel: Used for main structural components to ensure durability and load-bearing capacity.
- Corrosion-Resistant Coatings: Applied to protect against Singapore’s humid and corrosive environment.
Manufacturing Processes
- Welding: High-quality welding techniques ensure strong and reliable joints.
- Heat Treatment: Enhances material properties and eliminates internal stresses.
- Surface Treatment: Includes sandblasting, priming, and painting to improve corrosion resistance.
7. Safety Devices and Protective Measures
Limit and Anti-Collision Devices
- Limit Switches: Prevent over-travel of the crane.
- Anti-Collision Systems: Use sensors and alarms to avoid collisions with obstacles or other cranes.
Overload Protection
- Load Sensors: Monitor the load in real-time and trigger alarms or shut down the system if the load exceeds the rated capacity.
Electrical Safety Devices
- Leakage Protectors: Prevent electrical shocks and short circuits.
- Grounding Systems: Ensure safe electrical operation.
Maintenance and Repair Safety
Regular maintenance and inspections are conducted to ensure the crane’s long-term reliability. Safety protocols are strictly followed during maintenance activities.

8. Installation, Debugging, and Acceptance
Installation Preparation
- Site cleaning, equipment inspection, and personnel training are conducted before installation.
Installation Steps
- Foundation construction, equipment assembly, and system integration are carried out according to detailed plans.
Debugging and Testing
- Functional tests are performed to ensure all systems operate correctly.
- Safety tests are conducted to verify compliance with standards.
Acceptance Criteria
- The crane undergoes a comprehensive inspection and testing process before being approved for use.
9. Maintenance and Upkeep
Daily Maintenance
- Regular cleaning, lubrication, and inspection of components.
Fault Diagnosis and Troubleshooting
- Prompt identification and resolution of issues to minimize downtime.
Major Repairs and Upgrades
- Periodic overhauls and upgrades to maintain performance and extend service life.
Maintenance Plans and Records
- Detailed maintenance schedules and records are maintained to ensure consistent performance.
10. Conclusion
The 63/20t double girder overhead travelling crane is a vital asset for Singapore’s industrial and logistics sectors. Its advanced design, robust construction, and comprehensive safety features make it ideal for handling heavy loads in demanding environments. By adhering to international standards and incorporating cutting-edge technology, this crane ensures efficient, safe, and reliable operations, supporting Singapore’s position as a global leader in trade and industry.
For Singaporean businesses, investing in this crane means enhancing operational efficiency, ensuring safety, and achieving long-term cost savings. With proper installation, maintenance, and operation, the 63/20t double girder overhead travelling crane will deliver exceptional performance for years to come.