28-Mar-2025
Safe Operation Procedures for Electric Hoist of Overhead Crane (Single Girder Crane)
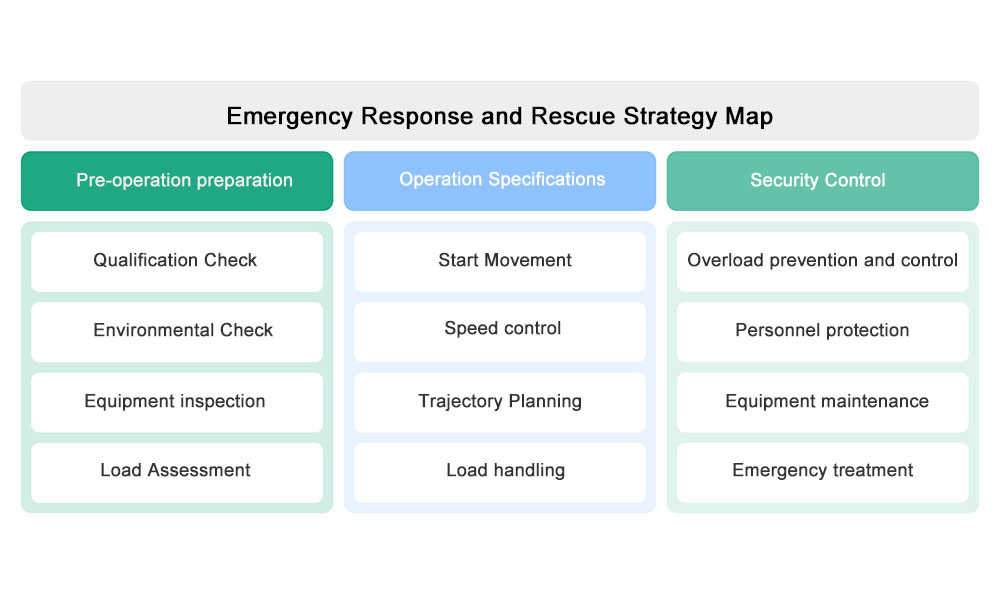
I. Pre-Operation Preparation and Inspection
1. Operator Qualifications and Requirements
- Operators must possess valid professional operation certificates and pass rigorous training assessments.
- Maintain good physical condition (vision, hearing, reaction ability, etc.). Strictly prohibit operation under the influence of alcohol or fatigue.
- Receive regular safety training (at least every 6 months) covering equipment operation, emergency procedures, and hazard identification.
- Wear appropriate personal protective equipment (PPE) including safety helmets, protective gloves, safety shoes, and high-visibility vests.
2. Equipment Appearance and Structural Inspection
- Electric Hoist Housing: Inspect for integrity, ensuring no severe wear, deformation, or cracks.
- Fasteners: Check all bolts, nuts, and other fastening components for tightness and absence of looseness or missing parts.
- Key Components:
- Wire ropes: Inspect for broken wires, corrosion, or deformation exceeding standards
- Sheaves and pulleys: Check for wear grooves exceeding 10% of rope diameter
- Hooks: Verify no cracks or throat opening increase exceeding 15%
- Brake system: Ensure proper lining thickness (minimum 50% of original)
- Conduct load testing with 125% of rated capacity annually, documented with certification.
3. Electrical System and Safety Device Inspection
- Power Circuitry:
- Verify insulation resistance >1MΩ (megohm) at 500V DC
- Check for exposed wiring or damaged insulation
- Ensure proper grounding with resistance <4Ω
- Control System:
- Test all push buttons for proper function
- Verify emergency stop functionality
- Check limit switches for proper operation
- Safety Devices:
- Overload protection: Calibrate to 110% of rated capacity
- Upper/lower limit switches: Test functionality
- Phase failure protection: Verify operation
- Emergency stop: Confirm immediate power cutoff
- Perform functional tests of all safety devices before each shift.
4. Load and Work Environment Assessment
- Load Characteristics:
- Precisely measure weight using certified scales
- Determine center of gravity for unbalanced loads
- Verify lifting points and rigging arrangements
- Work Environment:
- Minimum clearance: 0.5m above highest obstacle
- Floor load capacity: Verify ≥1.5 times maximum load
- Lighting: Maintain minimum 200 lux illumination
- Weather conditions: Cease operation at wind speeds >12.5 m/s (Beaufort 6)
- Conduct job safety analysis (JSA) for complex lifts, identifying all potential hazards.
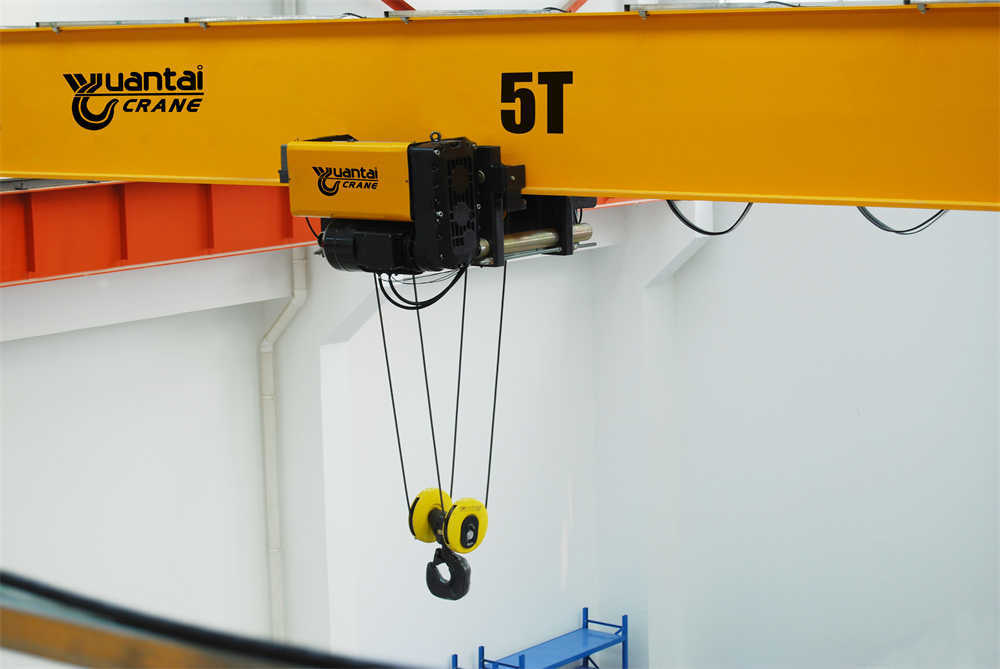
II. Operation Procedures and Specifications
1. Startup and Operation
- Pre-Operation Checklist:
- Verify all guards and covers in place
- Check lubrication levels
- Confirm unobstructed travel path
- Power-Up Sequence:
- Engage main disconnect
- Verify control voltage present
- Test emergency stop function
- Perform no-load test run
- Operating Parameters:
- Acceleration/deceleration: ≤0.3 m/s²
- Travel speed: ≤20 m/min (adjust per load)
- Hoisting speed: ≤8 m/min (variable frequency drives recommended)
- Implement “two-person verification” for critical lifts where visibility is limited.
2. Load Handling and Movement
- Lifting Preparation:
- Center load directly below hoist
- Apply slight tension to verify rigging
- Lift initially 100-150mm, pause to verify stability
- Movement Protocol:
- Maintain load height ≤1m during travel
- Use tag lines for load control when necessary
- Implement “no-go zones” marked with floor tape
- Special Conditions:
- Multi-crane lifts: Designate lift director
- High-temperature loads: Use appropriate slings
- Hazardous materials: Implement additional controls
- Utilize standardized hand signals or radio communication for all lifting operations.
3. Special Situation Management
- Power Failure:
- Engage manual release (if equipped)
- Lower load slowly using brake control
- Secure area until power restored
- Mechanical Failure:
- Activate emergency stop
- Notify maintenance immediately
- Post “Out of Service” tag
- Environmental Changes:
- Lightning: Cease operations within 8km
- Temperature extremes: Follow manufacturer limitations
- Reduced visibility: Implement additional spotters
- Maintain emergency response kit containing:
- Fire extinguisher (ABC type)
- First aid supplies
- Emergency lighting
- Communication devices
4. Shutdown Procedures
- Normal Shutdown:
- Lower load to designated area
- Raise hook to mid-position
- Move bridge to parking location
- Turn off main disconnect
- Post-Operation Inspection:
- Document any abnormalities
- Report maintenance needs
- Complete equipment log
- Lockout/Tagout:
- Apply personal lock during maintenance
- Verify zero energy state
- Test controls before restoring power
III. Safety Precautions and Risk Control
1. Overload and Eccentric Load Prevention
- Load Monitoring:
- Install certified load cells with digital display
- Implement automatic cut-off at 105% capacity
- Monthly calibration of weighing systems
- Load Stability:
- Maximum allowable angle: 3° from vertical
- Use spreader beams for wide loads
- Prohibit “side pulling” or shock loading
- Conduct quarterly load testing with certified weights to verify protection systems.
2. Personnel and Equipment Clearance
- Exclusion Zones:
- 360° perimeter: 1.5 times load dimension
- Overhead clearance: ≥2m from any structure
- Designated walkways clearly marked
- Access Control:
- Key-operated pendant controls
- Restricted area signage
- Motion sensors for automated warning
- Implement “three-point contact” rule when accessing work platforms.
3. Collision and Entanglement Prevention
- Anti-Collision Systems:
- Ultrasonic or laser-based sensors
- Bumper switches with automatic stop
- Rail end stops with energy absorption
- Rope Management:
- Daily inspection for “birdcaging” or kinks
- Proper spooling on drum (minimum 2 wraps)
- Replacement criteria per ISO 4309
- Install rotating hooks for loads requiring multiple turns.
4. Emergency Response and Rescue
- Emergency Protocols:
- Clearly posted evacuation routes
- Designated assembly points
- Trained first responders (minimum 10% of staff)
- Rescue Equipment:
- Man-rated fall protection
- Emergency lowering devices
- Confined space rescue kits
- Conduct biannual mock emergency drills covering:
- Load recovery procedures
- Personnel extraction
- Hazardous material spills
IV. Equipment Maintenance and Preservation
1. Routine Maintenance
- Daily Tasks:
- Visual inspection of structural components
- Function test of safety devices
- Lubrication of all moving parts
- Weekly Tasks:
- Brake adjustment verification
- Electrical connection tightening
- Rope lubrication (approved compounds only)
- Use predictive maintenance technologies including:
- Vibration analysis
- Thermography
- Oil analysis
2. Periodic Comprehensive Inspection
- Monthly Checks:
- Structural integrity (crack detection)
- Gearbox oil analysis
- Bearing wear measurement
- Annual Overhaul:
- Complete disassembly and inspection
- Non-destructive testing (NDT) of critical parts
- Paint system renewal
- Maintain computerized maintenance management system (CMMS) tracking:
- Service history
- Component life cycles
- Failure trends
3. Component Replacement and Upgrades
- Replacement Criteria:
- Hooks: At any crack or 15% throat opening
- Wire ropes: Per ISO 4309 discard standards
- Contactors: After 100,000 operations
- Modernization Options:
- Variable frequency drives
- Remote monitoring systems
- LED lighting upgrades
- Implement engineering controls to reduce maintenance hazards:
- Permanent platforms for access
- Fall arrest anchor points
- Tool tethering systems
4. Documentation and Record Keeping
- Required Records:
- Daily inspection logs (retain 3 years)
- Maintenance reports (retain for equipment life)
- Training certifications (current copies)
- Regulatory Compliance:
- OSHA 1910.179 documentation
- ANSI/ASME B30 standards
- Local jurisdiction requirements
- Utilize digital documentation systems with:
- Cloud backup
- Mobile access
- Automated reminders
V. Conclusion and Continuous Improvement
The safe operation of electric hoists for overhead cranes requires strict adherence to comprehensive procedures encompassing personnel competency, equipment integrity, proper operating techniques, and robust maintenance practices. Organizations must implement a holistic safety management system that includes:
- Competency Assurance:
- Tiered certification programs
- Knowledge verification testing
- Scenario-based evaluations
- Technology Integration:
- IoT-enabled monitoring
- Augmented reality training
- Predictive analytics
- Cultural Development:
- Safety observation programs
- Near-miss reporting systems
- Behavioral-based safety initiatives
- Performance Metrics:
- Leading indicators (inspection completion rates)
- Lagging indicators (incident rates)
- Equipment reliability metrics
By implementing these enhanced procedures and maintaining rigorous compliance standards, organizations can achieve optimal balance between operational efficiency and workplace safety. Regular review cycles (at minimum annually) should evaluate procedure effectiveness and incorporate technological advancements, regulatory updates, and lessons learned from industry incidents.
This document represents minimum requirements and should be supplemented with manufacturer-specific recommendations and site-specific hazard assessments. All personnel must acknowledge understanding of these procedures through formal training documentation before operating any overhead crane equipment.