13-Mar-2025
Safety technical requirements for bridge cranes
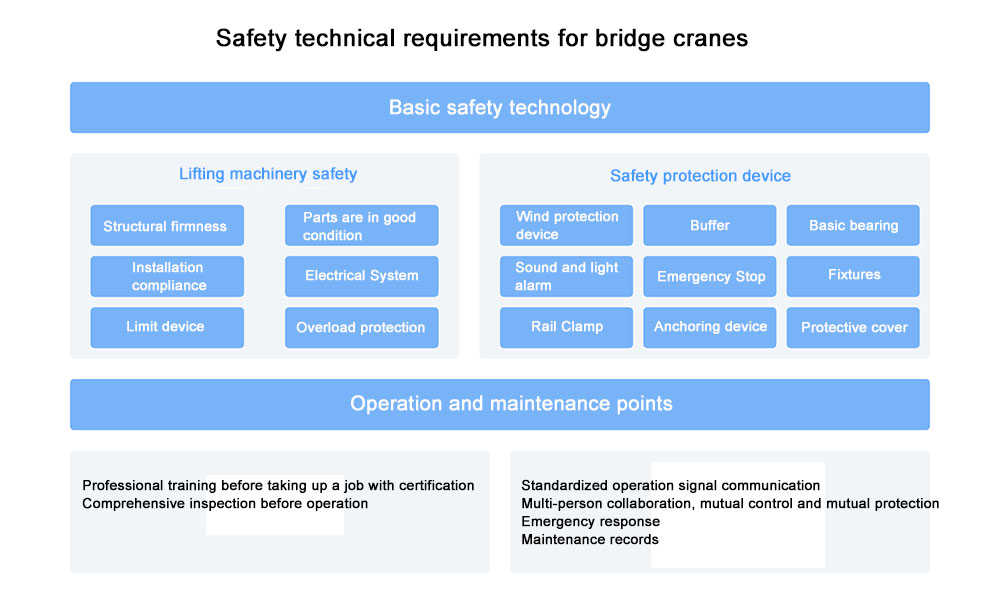
As an indispensable equipment in industrial production, the safety and technical requirements of bridge cranes are directly related to production efficiency and personnel safety. These requirements are strictly regulated in many aspects such as the crane itself and its installation, safety device configuration, operation and use, and maintenance. From the structural firmness and integrity of the crane’s parts, to the standardization of the installation process, to the safety of the electrical system, every link must be strictly controlled. In addition, the reasonable configuration of safety devices such as limit devices, overload protection, and windproof devices is also the key to ensuring the safe operation of the crane. For operators, certification, professional training, and careful inspection before operation are all basic requirements to ensure operational safety. At the same time, daily maintenance and regular inspection of the crane, as well as professional repair and treatment in the event of a fault, should not be ignored.
Crane itself and installation requirements
Structural firmness and integrity of parts
As an indispensable lifting equipment in industrial production, the structural firmness of bridge cranes is the key basis for ensuring safe and efficient operation. During the design and manufacturing process, the main load-bearing components such as the main beam, end beam, and outriggers must be made of high-quality steel with high strength, high toughness, and excellent fatigue resistance, such as Q345B or higher-grade low-alloy structural steel. This type of steel can not only withstand the static and dynamic loads in daily operations, but also maintain stable mechanical properties in long-term use, effectively preventing deformation or fracture caused by stress concentration.
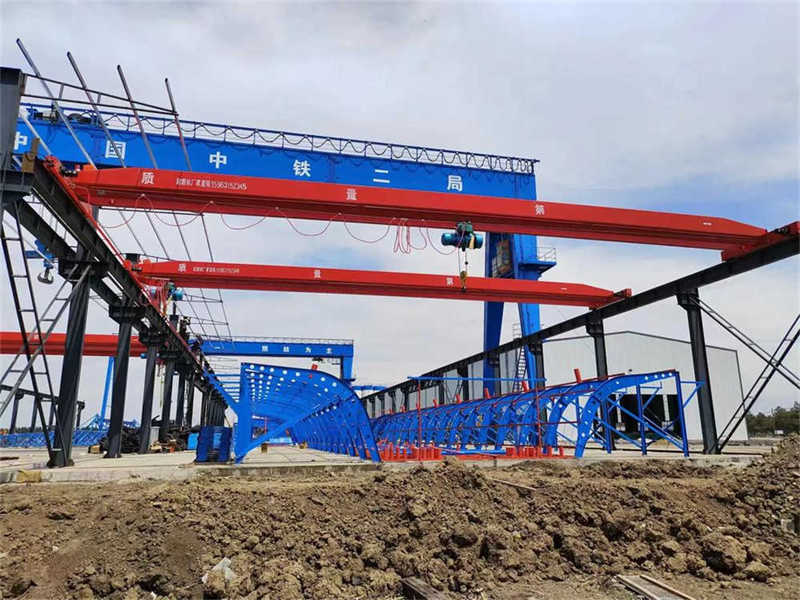
As the main component for carrying heavy objects, the main beam must fully consider the mechanical distribution in its structural design to ensure that it can maintain good bending and torsional stiffness under full load or overload conditions to avoid flexural deformation. The end beam should have sufficient rigidity to maintain the accuracy and stability of the crane’s operating track. The outrigger design must consider the ground bearing capacity to ensure that the entire machine will not overturn or become unstable when lifting heavy objects. All these key components must undergo strict welding processes and heat treatment processes during the manufacturing process to ensure the quality of the welds and eliminate welding stress, thereby improving the overall strength and stability of the entire structure.
In addition to the main frame structure, other parts of the crane, such as pulleys, wire ropes, drums, brakes, etc., must also be kept intact. The pulleys should be inspected and maintained regularly to ensure that they rotate flexibly and the bearings are free of wear to reduce the friction loss between the rope and the pulley; the wire rope, as a key load-bearing component of the crane, needs to be regularly inspected and replaced in accordance with relevant national standards to avoid strength loss due to internal fatigue damage; the drum should have good winding performance to prevent the wire rope from being disordered or out of the groove; the brake, as a safety protection device, must be regularly checked for its braking performance to ensure that it can effectively stop the falling of heavy objects or the shaking of the sling in an emergency.
During the installation process, all parts must be installed in accordance with the design drawings and national standards. For example, the laying of the track must ensure that its straightness, levelness and elevation meet the requirements to avoid unstable operation of the crane due to uneven tracks; during foundation construction, the bearing capacity, stability and earthquake resistance requirements must be fully considered to ensure that the foundation is firm and reliable. After assembly, strict debugging work is required to conduct a comprehensive test of the various performance indicators of the crane to ensure that it meets the design requirements.
Installation Standardization
When installing a bridge crane, a strict standard process must be followed. This includes the laying of crane tracks, foundation construction, crane assembly and commissioning. Track laying must ensure that the straightness, levelness and elevation meet the requirements, and foundation construction must ensure sufficient bearing capacity and stability. During the assembly process, the connection of each component must be tight and reliable, and during commissioning, the performance indicators of the crane must be fully tested to ensure that it meets the design requirements.
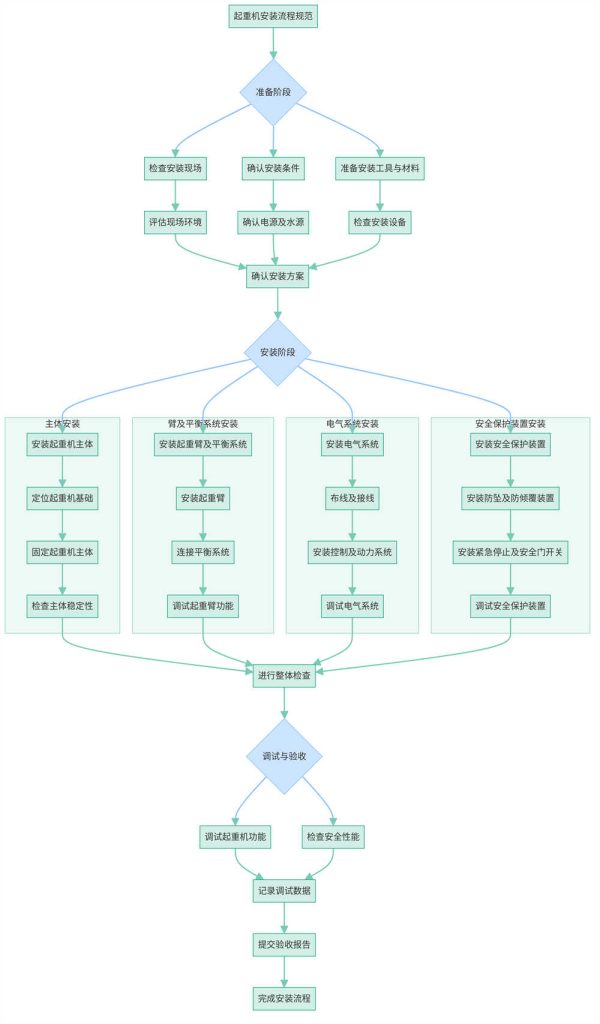
Electrical system safety
The electrical system is an important part of the bridge crane, and its safety is directly related to the operation stability of the crane and the safety of the operator. The electrical system should have good insulation performance, all electrical components must comply with national standards, and the wiring must be standardized and firm. In addition, the crane should be equipped with electrical safety devices such as overload protection, short circuit protection, and grounding protection to prevent safety accidents caused by electrical failures.
Safety device configuration
Limit device and overload protection
The limit device is an important part of the safe operation of the bridge crane, and is mainly used to prevent the crane from exceeding the preset working range during operation. These devices are equipped with limit switches on the running direction of the trolley and the trolley and the lifting height. When the crane approaches the limit position, the limit switch can automatically cut off the power supply and stop the crane from running, thereby avoiding equipment damage or safety accidents caused by misoperation or unexpected situations.
Overload protection device is also indispensable, which can monitor the load of the crane in real time. Once the crane is overloaded, the device will immediately sound an alarm and cut off the power source to prevent structural damage or overturning accidents caused by overload.
Windproof device configuration
In areas with strong winds or in open-air working environments, bridge cranes need to be equipped with windproof devices. These devices usually include track clamps, anchoring devices or windproof chains, which can fix the crane under strong winds to prevent it from moving or overturning due to wind force.
Other safety devices
In addition to limit devices and overload protection devices, bridge cranes should also be equipped with other necessary safety devices. For example, buffers, sound and light alarm devices, emergency stop buttons, etc. The buffer can absorb the impact energy of the crane during a collision, the sound and light alarm device can send out a warning signal when the crane is running, and the emergency stop button allows the operator to quickly cut off the power supply in an emergency to ensure safety. The configuration and application of these devices provide a strong guarantee for the safe operation of bridge cranes.
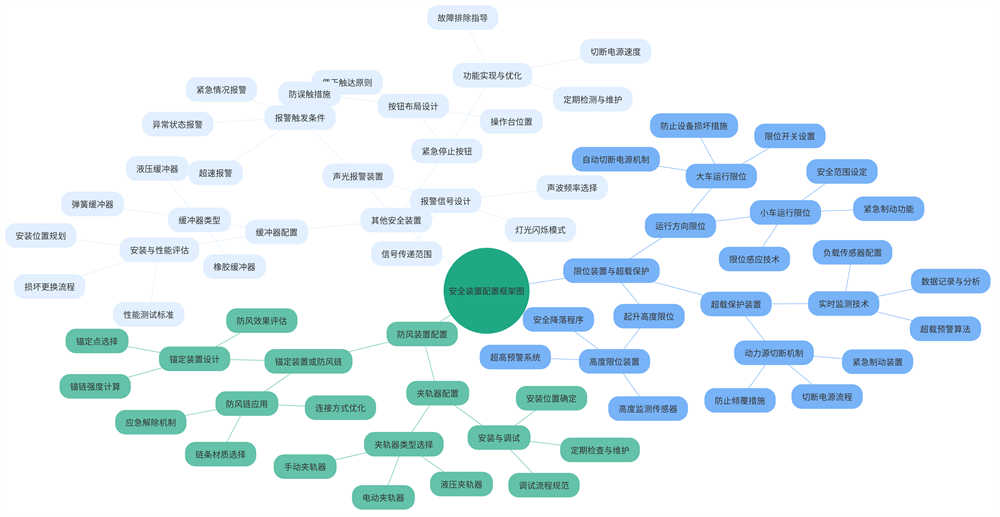
Operation and use requirements
Certification and professional training
As an important lifting equipment, the operators of bridge cranes must undergo strict professional training and obtain the operation certificate issued by the relevant national departments before they can engage in related work. The training content should cover the structural principles, operating procedures, safety knowledge and emergency handling of bridge cranes to ensure that operators have a deep understanding and mastery of the equipment. Through professional training, operators can not only master the operation skills of bridge cranes, but also improve safety awareness and enhance the ability to warn and prevent potential dangers, thereby effectively reducing the occurrence of operating errors and accidents.
Pre-operation inspection and standardized operation
Before each operation, the operator of the bridge crane should conduct a comprehensive and detailed inspection of the equipment. This includes inspection of the electrical system, such as checking whether the wires and cables are intact and whether the control system is normal and reliable; inspection of mechanical parts, such as checking whether the hooks, wire ropes, etc. are worn or broken; inspection of safety devices, such as checking whether the limiters, buffers, etc. are sensitive and effective. Only after confirming that all parts of the equipment are intact can the operation begin. At the same time, during the operation, the operator must strictly abide by the operating procedures and operate according to the prescribed procedures and signals. For a multi-person collaborative operation environment, a good signal communication mechanism should be established between operators to ensure accurate and timely information transmission. In addition, operators must always be vigilant and pay attention to the operating status of the crane and changes in the surrounding environment. Once an abnormal situation or potential danger is found, measures should be taken immediately to deal with or report it to ensure the safe and smooth operation.
Signal communication and careful observation
In a multi-person collaborative operation environment, good signal communication should be maintained between the operator of the bridge crane and the ground commander or other relevant personnel. Through clear and accurate signal transmission, coordination and safety during the operation can be ensured. At the same time, operators also need to be vigilant at all times and pay attention to the operating status of the crane and changes in the surrounding environment. For any abnormal situation or potential danger found, the operator should immediately take measures to deal with or report it to ensure the safe and smooth operation.
Maintenance requirements
Daily maintenance and regular inspections
Daily maintenance and regular inspections of bridge cranes are the key to ensuring their long-term stable operation. Daily maintenance work includes cleaning, lubrication, tightening, etc., which can effectively extend the service life of the crane. Regular inspection is even more important. It requires comprehensive inspection of various performance indicators of the crane, including electrical systems, hydraulic systems, structural parts, etc., to ensure the safety and reliability of the crane. These inspections should be carried out by professionals and recorded for traceability and analysis.
Fault repair and professional handling
When a crane fails, the operator should stop using it immediately and report it to the maintenance personnel. The maintenance personnel need to conduct professional analysis of the fault, determine the cause of the fault and formulate a maintenance plan. During the maintenance process, the safety operating procedures should be strictly followed to ensure the safety of the maintenance personnel. At the same time, major faults or safety hazards should be reported to the superior department in a timely manner so that further measures can be taken to deal with them. In addition, for some complex fault problems, multi-departmental collaborative processing is required to ensure the smooth progress of maintenance work.
Fault maintenance record
Serial number | Device name | Fault description | Time of failure | Maintenance personnel | Maintenance measures | Maintenance completion time | Note |
1 | Bridge crane | Electrical system failure | 2023-05-01 | Replace damaged parts, check wiring connections | 2023-05-02 | Major failures, multi-department collaboration | |
2 | Bridge crane | Hydraulic system oil leakage | 2023-06-15 | Replace the sealing ring and check the hydraulic oil level | 2023-06-16 | _ | |
3 | Bridge crane | Loose structural parts | 2023-07-20 | Fasten loose parts and check the overall structure | 2023-07-20 | Problems found during daily inspections | |
4 | Bridge crane | Control system failure | 2023-08-10 | Reset the control system and check the sensor status | 2023-08-11 | Emergency repairs to ensure equipment safety |
Regular maintenance record form (related to fault repair)
Serial number | Device name | Maintenance date | Maintenance content | Maintenance staff | Next maintenance plan | Note |
1 | Bridge crane | 2023-04-30 | Clean, lubricate, tighten | 2023-07-30 | _ | |
2 | Bridge crane | 2023-07-30 | Comprehensive inspection of electrical and hydraulic systems | 2023-10-30 | Discover potential faults and handle them promptly | |
3 | Bridge crane | 2023-10-30 | Check the structural parts and replace the seriously worn parts. | 2024-01-30 | _ | |
4 | Bridge crane | 2024-01-30 | Comprehensive detection of control systems and safety devices | 2024-04-30 | _ |