15-May-2025
Workshop Cranes for Manufacturing & Automotive: Boosting Efficiency & Safety
Introduction
In automotive and manufacturing plants, workshop cranes are critical for moving heavy components, optimizing assembly lines, and reducing worker strain. Whether handling engine blocks, stamping dies, or robotic welding cells, the right crane system improves productivity, precision, and workplace safety.
This guide covers:
✅ Best crane types for automotive & manufacturing
✅ How automation enhances production lines
✅ Key features for precision handling
✅ Safety standards & maintenance best practices
Why Manufacturing & Automotive Plants Need Specialized Cranes
Manual lifting in production environments leads to:
✖ Slow cycle times (bottlenecks in assembly)
✖ High injury risk (back strains, crushed limbs)
✖ Product damage (from improper handling)
✖ Downtime (fatigue-related slowdowns)
The right crane system solves these challenges by:
✔ Accelerating material flow (3x faster than forklifts)
✔ Enabling precise positioning (±1mm accuracy for robotic integration)
✔ Reducing labor costs (1 operator can manage multiple lifts)
✔ Improving ergonomics (eliminating heavy manual lifts)
Best Crane Types for Manufacturing & Automotive
1. Bridge Cranes (Overhead Cranes) – For Heavy Assembly Lines
Best for: Large parts handling (chassis, presses, molds)
Capacity: 5–100+ tons
Key Benefits:
- Full coverage of production floor
- High-speed hoists (up to 180 m/min)
- Automation-ready (sync with robotic arms/AGVs)
- Custom spans (10m–50m+)
Ideal Uses:
- Stamping press servicing
- Engine block transfers
- Robotic cell loading
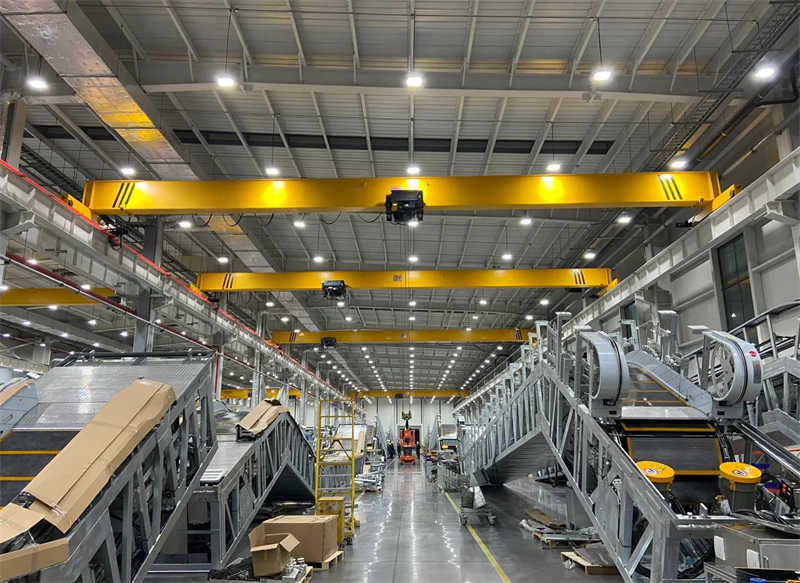
2. Jib Cranes – For Workstation Precision
Best for: Assembly stations, machining centers
Capacity: 0.5–10 tons
Key Benefits:
- 360° rotation for flexible positioning
- Compact footprint (fits between machines)
- Plug-and-play electric chain hoists
Ideal Uses:
- Transmission assembly
- CNC machine loading
- Welding cell component handling
3. Gantry Cranes – For Flexible Plant Layouts
Best for: Plants with changing floor plans
Capacity: 1–50 tons
Key Benefits:
- Mobile (no permanent installation)
- Wide spans (up to 20m for body panels)
- Outdoor-capable (paint shop transfers)
Ideal Uses:
- Vehicle frame handling
- Die changes in press shops
- Crossover between buildings
4. Smart Hoists – For Automated Production
Best for: Industry 4.0 integration
Features:
- Load sensors (prevent overloads)
- IoT connectivity (real-time monitoring)
- Programmable paths (repeatable movements)
Ideal Uses:
- Just-in-sequence part delivery
- Battery pack installation (EV manufacturing)
- Precision sub-assembly placement
Key Features for Manufacturing Cranes
When selecting a crane for automotive/manufacturing, prioritize:
🔹 Precision Control
- Variable-speed hoists (±1mm positioning)
- Anti-sway systems for delicate components
🔹 Automation Readiness
- PLC interfaces for robotic handoffs
- Barcode/RFID scanning for traceability
🔹 Durability
- IP54+ ratings for weld shop environments
- Fatigue-rated components for 24/7 operation
🔹 Safety Compliance
- EN 13001 / OSHA standards
- Emergency stop + overload protection
Case Study: How [Auto Supplier X] Reduced Changeover Time by 60%
A Tier 1 stamping plant implemented motorized jib cranes with:
- Tooling quick-releases for die changes
- Preset height stops for repeatability
- RFID-tagged fixtures
Results:
✔ 60% faster die changes
✔ Zero handling-related defects
✔ ROI in 8 months
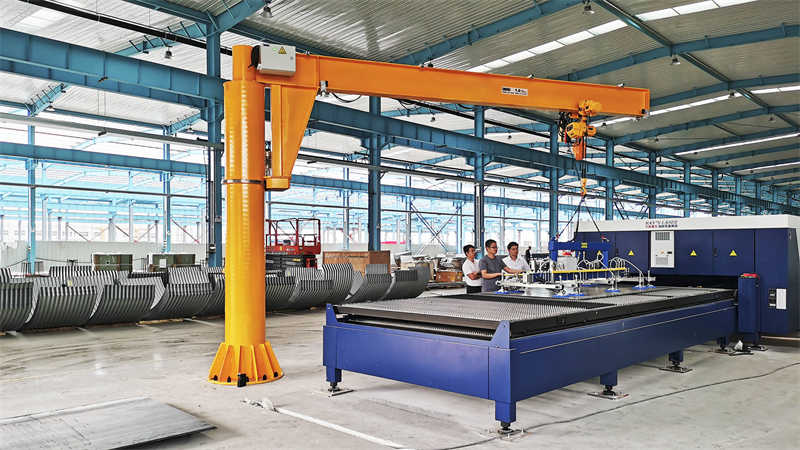
Choosing the Right Crane for Your Plant
Ask these questions:
- What’s your heaviest component? → Include future model plans
- How precise must positioning be? → ±1mm vs ±10mm requirements
- Indoor or outdoor use? → Paint/powder coat compatibility
- Manual or automated? → ROI on automation is <2 years for high-volume
Final Recommendations
- Best for Stamping/Press Shops: Bridge cranes (heavy dies)
- Best for Assembly Lines: Smart jib cranes (precision placement)
- Best for Flexible Layouts: Gantry cranes (reconfigurable lines)
Need Help Specifying?
➡ Our automotive crane specialists offer free plant assessments.