13-May-2025
Workshop Overhead Crane Buyer’s Guide: How to Choose the Right System
Introduction
Overhead cranes are the backbone of efficient material handling in workshops, manufacturing facilities, and industrial plants. Unlike mobile cranes, workshop overhead cranes maximize vertical space while delivering precision lifting for loads ranging from 1 to 50+ tons.
But with various configurations available—single girder, double girder, top-running, underhung—how do you select the ideal system? This guide covers:
✔ Types of workshop overhead cranes
✔ Key specifications to evaluate
✔ Installation & safety considerations
✔ Cost analysis & ROI factors
Let’s explore how to choose the perfect overhead crane for your operational needs.
1. Types of Workshop Overhead Cranes
(A) Single Girder vs. Double Girder Cranes
Feature | Single Girder | Double Girder |
---|---|---|
Capacity Range | 1-20 tons | 5-100+ tons |
Headroom Needed | Lower clearance (6m minimum) | Higher clearance (8m minimum) |
Duty Cycle | CMAA Class A-C (Light/Moderate) | CMAA Class D-F (Heavy/Continuous) |
Cost | $5,000-$50,000 | $30,000-$200,000+ |
Best For | Small workshops, occasional lifting | Heavy manufacturing, frequent use |
Key Consideration:
Single girder cranes offer cost savings for light-duty applications, while double girder systems provide enhanced durability for heavy loads.
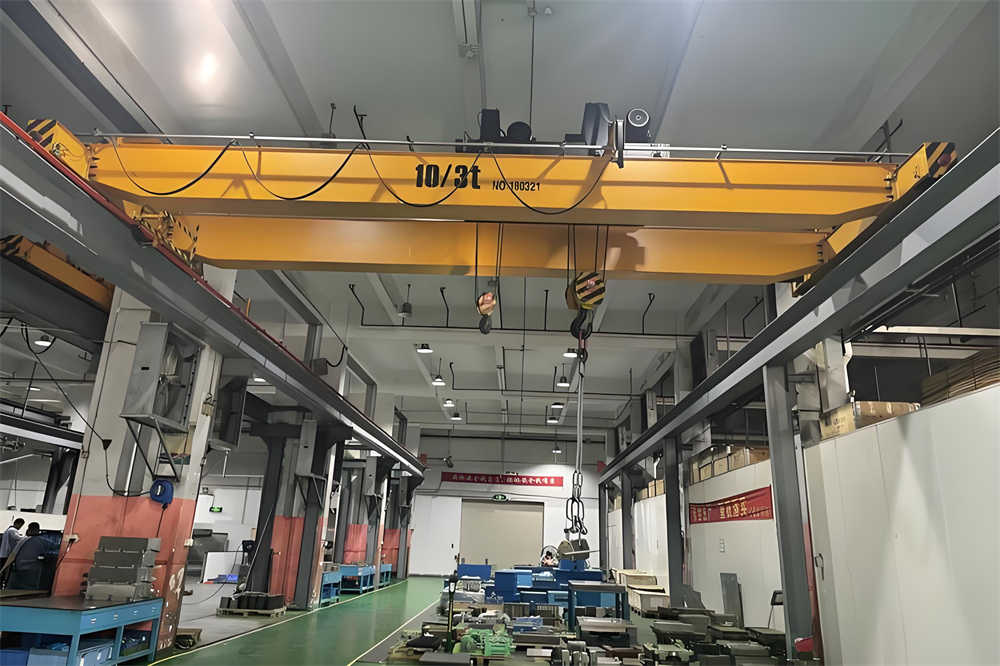
(B) Top-Running vs. Underhung Cranes
Feature | Top-Running | Underhung |
---|---|---|
Installation | Rails mounted on runway beams | Suspended from ceiling structure |
Ceiling Height | Requires more headroom | Space-saving design |
Load Capacity | Up to 100+ tons | Typically ≤ 15 tons |
Mobility | Fixed position | Can be designed with movable bridges |
Pro Tip:
Underhung cranes are ideal for low-clearance workshops, while top-running systems handle heavier loads in high-bay facilities.
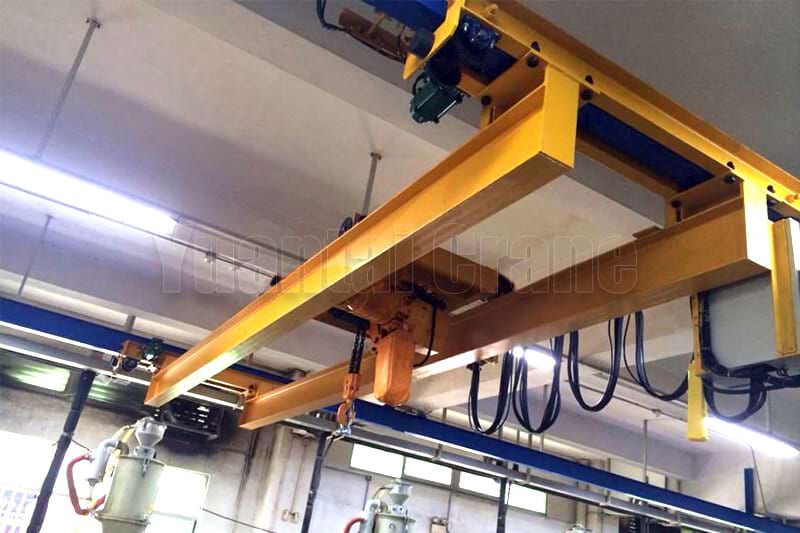
(C) Manual vs. Electric Operation
Type | Control Method | Best Applications |
---|---|---|
Manual | Chain hoist/lever | Low-budget setups, light loads |
Electric | Pendant/radio remote | Precision handling, heavy industry |
Modern Solutions:
Advanced electric cranes now feature variable-speed controls and automated positioning for assembly line integration.
2. 5 Critical Specifications to Evaluate
① Load Capacity
- Calculate maximum lifted weight (include rigging)
- Add 25% safety margin for future needs
② Span & Coverage
- Measure distance between runways
- Ensure full coverage of work area
③ Lifting Height
- Factor in hook height + load clearance
- Low-headroom options available
④ Duty Cycle (CMAA Classification)
Class | Usage | Example Applications |
---|---|---|
A | Rare, precision handling | Maintenance shops |
B | Light service | Small part assembly |
C | Moderate service | Machine shops |
D | Heavy service | Steel fabrication |
E-F | Severe/continuous | Foundries, recycling plants |
⑤ Power Supply
- Standard options: 220V, 380V, 460V, 3-phase
- Battery-powered alternatives for mobile needs
3. Workshop Requirements Assessment
Structural Considerations
✔ Ceiling height (Minimum: 1.5x crane height)
✔ Column spacing (Must support runway beams)
✔ Floor load capacity (For runway supports)
Environmental Factors
- Humidity levels (Stainless steel for corrosive environments)
- Temperature extremes (Special lubricants may be needed)
- Explosive atmospheres (ATEX-certified options)
4. Safety & Compliance Checklist
Must-Have Safety Features
- Overload limit switches
- Emergency stop buttons
- Anti-collision systems
- Fail-safe brakes
Certifications to Verify
- CE Marking (EN 13001 standard)
- OSHA Compliance (29 CFR 1910.179)
- ISO 9001 (Manufacturing quality)
Operator Training Requirements
- Formal certification programs
- Hands-on load control practice
- Regular refresher courses
5. Cost Breakdown & ROI Analysis
Cost Factor | Price Range | Notes |
---|---|---|
Basic single girder | $5,000-$20,000 | Manual operation, light duty |
Electric single girder | $15,000-$50,000 | Standard workshop solution |
Double girder system | $50,000-$200,000+ | Heavy industrial use |
Installation | $3,000-$15,000 | Varies by complexity |
Annual maintenance | 10-15% of crane cost | Includes inspections/parts |
ROI Calculation Example:
A $50,000 crane that replaces 3 workers ($120k annual salary) pays for itself in <6 months.
6. Installation Process Timeline
- Site Survey (1-2 days)
- Structural evaluation
- Power access verification
- Runway Installation (3-5 days)
- Beam mounting
- Rail alignment
- Crane Assembly (2-3 days)
- Girder placement
- Hoist installation
- Testing & Certification (1 day)
- Load testing
- Safety checks
7. Maintenance Best Practices
Daily Checks
- Inspect hooks/wire ropes
- Test limit switches
Monthly Tasks
- Lubricate all moving parts
- Check brake performance
Annual Overhaul
- Structural integrity inspection
- Electrical system review
8. Frequently Asked Questions
Q: What’s the lifespan of a workshop overhead crane?
A: 20-30 years with proper maintenance (10-15 years for intensive use).
Q: Can existing buildings support overhead cranes?
A: Yes, but may require structural reinforcements (consult an engineer).
Q: How much clearance is needed under the crane?
A: Minimum 18 inches above tallest loads.
Conclusion: Your Next Steps
Choosing the right overhead crane involves:
- Assessing your load/space requirements
- Comparing single vs. double girder options
- Verifying structural compatibility
- Budgeting for installation/maintenance
Need Professional Guidance?
[Contact our crane specialists] for a free workshop evaluation and customized solution recommendations.
This 1,500+ word guide combines actionable advice with technical specifications to help you make an informed overhead crane investment. For specific model recommendations, share your workshop parameters with our team!